FRP grating (with or without a grating cover) and FRP plate are versatile and widely used materials...
Know Your FRP Applications: Open Grating, Grating Cover, and FRP Plate
FRP grating (with or without a grating cover) and FRP plate are versatile and widely used materials for industrial applications. Covered grating is a strong platform, while open grating offers strength while also allowing for drainage and ventilation. Fiberglass reinforced plastic plate is a durable and weather resistant covering for areas that need to be resistant to corrosion.
Choosing the right type of FRP product helps you with successful design and deployment in the field. Understanding the functional strengths and weaknesses of covered grating vs. open grating ensures you get the most out of your investment. This guide will explore the advantages and disadvantages of both types of grating, along with real-world scenarios to help you make the appropriate choice.
Understanding FRP Plates vs. Grating Covers
Covered grating is an augmented version of our popular grating products that is equipped with a slip-resistant floor plate to provide a solid walking surface. This add-on covering makes it possible to customize grating for various industrial and commercial applications. This type of product provides approximately 30% higher stiffness than open mesh grating.
FRP structural plates (sometimes referred to fiberglass plates) are made from fiberglass embedded in a molded resin matrix. They are solid plates of FRP in various colors that can be cut to the desired size and shape. Fiberglass plates can be used as a standalone product for applications such as flooring when an open mesh is not required. This specially designed product is nonporous, easily cleaned by a high-pressure washer, and can withstand cleaning solutions.
Benefits of Molded or Pultruded FRP with a Grating Cover
Increased Stability and Load-Bearing Capacity: A solid top distributes weight more evenly across the underlying grating, enhancing its load-bearing capabilities. This makes covered grating ideal for heavy-duty industrial environments like factories and warehouses that can handle significant foot traffic and equipment loads.
Prevents Contamination of Work Surfaces Below: The solid top acts as a barrier, preventing debris, spills, and liquids from falling through the grating and contaminating work areas underneath. This can be helpful in applications like food processing facilities, laboratories, and pharmaceutical plants. Of course, this depends on how the area is cleaned. Some food and beverage plants use elevated open grating for work platforms and spray clean underneath them.
Helps Control Subsurface Odors: Some industrial processes can generate unpleasant odors. Grating covers help contain these odors by preventing them from rising through the open spaces of traditional grating.
Level Surface for Cart and Foot Traffic: The solid top surface creates a smooth, slip-resistant surface that offers a less bumpy ride for wheeled carts. A solid surface may be particularly beneficial for areas with high foot traffic. It is an extra precaution for site visitors who may wear shoes with narrow heels which could get caught in open grating. Additionally, the solid top prevents objects from falling through the grating, minimizing trip hazards.
-
Use cases for pultruded covered grating include utility trench covers.
-
Molded covered grating is often used over walkways over tank tops and vats.
Exploring Open Grating
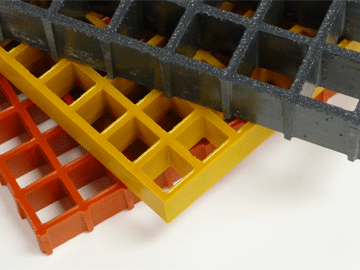
FRP open grating
Open grating, the more traditional type of FRP flooring, features a grid-like design with bars spaced close together for structural strength.
This open design offers distinct advantages:
Allows for Natural Drainage and Ventilation: Liquids and debris easily pass through the openings, preventing them from accumulating on the surface. This makes open grating ideal for outdoor applications where water drainage is essential. These characteristics make it ideal for outdoor walkways, trenches, and platforms. Additionally, the open design allows for air circulation which can be beneficial in promoting a cooler work environment in indoor spaces.
Lightweight and Easy to Install: Open grating is lighter than its solid counterpart, making it easier to transport and install. This can be a significant advantage in large-scale projects or situations where weight limitations exist.
Allows Sunlight to Penetrate: Open grating allows sunlight to pass through, which is crucial for promoting healthy marine life in applications like docks, piers, and boathouses. In some cases, this may be a regulatory requirement in marine applications.
Factors Influencing the Choice Between Open Grating and FRP with a Grating Cover
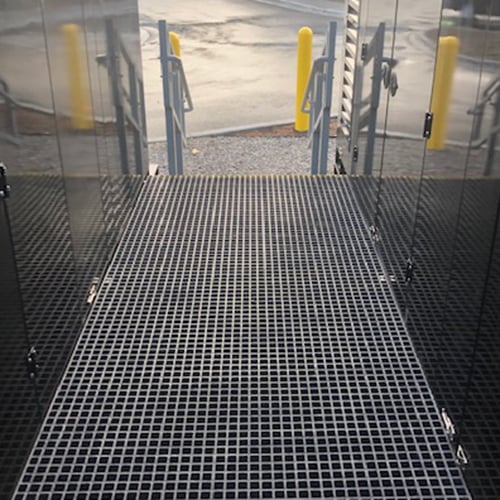
FRP service platform for generators
Choosing between covered grating and open grating hinges on several key factors:
Load Requirements and Structural Considerations: Consider the weight the grating will need to support. For heavy-duty applications, there are high load pultruded gratings that are designed specifically for heavy-turning traffic (such as forklifts).
Environmental Factors: Think about exposure to chemicals, weather, or corrosion. Fiberglass from Fibergrate excels in corrosion resistance, making both covered grating and open grating ideal for harsh environments; however, open grating may be preferable in situations requiring maximum airflow or minimizing ice buildup.
Safety Regulations and Standards: Specific safety regulations might dictate the type of grating needed. For instance, some areas may require slip-resistant surfaces or a solid top to prevent objects from falling through.
Cost-Effectiveness and Long-Term Maintenance: Evaluate the initial cost of the grating material and installation alongside potential maintenance needs. While open grating might have a lower upfront cost, its open design may require more frequent cleaning to prevent debris buildup. Covered gratings, with their solid surface, might require less frequent cleaning but may have a slightly higher initial cost.
Benefits and Uses of FRP Plate Products
Fiberplate is a molded FRP product that is highly corrosion resistant, even more so than stainless steel. It is slip resistant which makes it an optimal choice in wet or slippery environments. Available in thicknesses from ⅛” to ¾”, it has some load bearing capacity, but is not a substitute for grating for areas with a high volume of heavy traffic. Like Fibergrate’s grating products, FIberplate is lightweight and easy to install using power hand tools.
Applications for fiberglass reinforced plate include car washes and other environments where there are caustic chemicals in use.
Which FRP Product Is Right for Your Project?
Consulting with a qualified FRP structural engineer is highly recommended. They can assess your specific needs and recommend the optimal grating solution for your application, considering factors like load requirements, environmental conditions, safety regulations, and cost-effectiveness.
For more information, read through our covered grating brochure.
Topics: FRP, Safety, Molded Grating