Fiberglass reinforced plastics are versatile materials used in an ever-increasing array of...
The Making of Fiberglass Reinforced Plastics
Fiberglass reinforced plastics are versatile materials used in an ever-increasing array of applications, from industrial equipment and chemical processing to consumer goods. But have you ever wondered how these strong and lightweight materials are made?
Here is a look at the manufacturing process for FRP.
Manufacturing Process for Pultruded Fiberglass-Reinforced Plastic
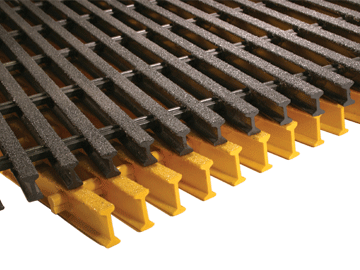
Fibergrate pultruded grating
Pultrusion is the primary method for creating FRP products with continuous profiles, such as rods, bars, beams, and channels. It is also used to produce FRP grating with a high load capacity. Here is a simplified overview of the process:
- Selection of Materials: The process begins with selecting the appropriate resin and fiberglass materials based on the desired properties of the final product. Depending on the application, the resin can be polyester, vinyl ester, or epoxy.
- Preparation of Fiberglass: Fiberglass, typically in the form of rovings (bundles of continuous glass filaments), mats, or fabrics, is pulled through a resin bath to embed it with the chosen resin. This ensures that the fiberglass is thoroughly coated with resin for optimal strength and durability.
- Pultrusion: The coated fiberglass is then pulled through a series of heated dyes or molds. These dyes shape the composite material into the desired profile or cross-section while curing the resin. The pultrusion process is continuous, meaning that the material is pulled through the dyes at a constant rate for a uniform result.
- Curing: As the coated fiberglass passes through the heated dyes, the resin undergoes curing, which involves a chemical reaction that transforms it from a liquid to a solid state. The exact temperature and curing time depend on the specific resin system being used.
- Cutting and Finishing: Once the pultruded profile has been cured and cooled, it is cut to the desired length and undergoes any necessary finishing processes, such as trimming or sanding, to achieve the final dimensions and surface quality.
- Quality Control: Throughout the manufacturing process, quality control measures are implemented to ensure that the finished FRP products meet the required specifications and standards for strength, appearance, and other performance characteristics.
Check out Fibergrate’s pultruded FRP products to see the end result.
Manufacturing Process for Molded Fiberglass Reinforced Plastics
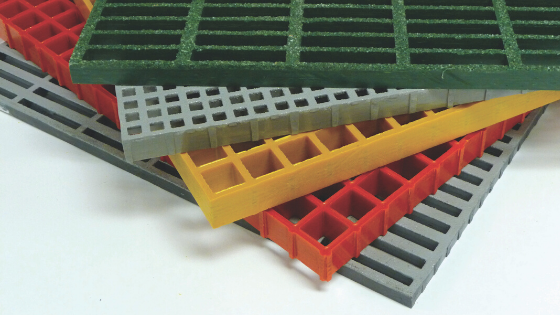
Fibergrate FRP grating
For more complex shapes and parts, a process called compression molding is often used:
- Preparation of Materials: Like in pultrusion, the process starts with selecting the appropriate resin and fiberglass materials based on the desired properties of the final product. Resins commonly used include polyester, vinyl ester, or epoxy, depending on factors like strength, corrosion resistance, and cost. Fiberglass reinforcements can be in the form of chopped strands, mats, or fabrics.
- Mold Preparation: A mold, usually made of metal or composite materials, is prepared. The mold is typically in two halves to allow for easy removal of the finished product. It is cleaned and treated with a release agent, before laying the fiberglass reinforcement material, to prevent the composite from sticking to the mold surface.
- Laying Up: Layers of the fiberglass reinforcement material are manually or automatically laid up inside the mold cavity according to the desired thickness and orientation. This step can involve applying resin to the reinforcement layers as they are placed to ensure thorough impregnation.
- Compression: Once the desired number of layers has been laid up, the mold is closed and pressure is applied to compact the layers and remove any trapped air. Compression can be achieved through hydraulic presses, mechanical presses, or other methods, depending on the size and complexity of the part.
- Curing: With the mold closed and under pressure, the composite is cured. This involves initiating the resin curing process, either through the application of heat, chemical catalysts, or a combination of both. The curing process may take several hours to complete, depending on the resin system and part size.
- Demolding: After the curing process is complete, the mold is opened, and the finished FRP part is removed. Care must be taken during demolding to avoid damaging the part or the mold.
- Finishing: Once removed from the mold, the molded FRP part may undergo additional finishing processes, such as trimming excess material, sanding, painting, or coating, to achieve the desired surface finish and dimensional accuracy.
- Quality Control: Like pultruded FRP, stringent quality control measures are implemented throughout the manufacturing process to verify that the finished products consistently meet or exceed the required specifications.
You can explore Fibergrate’s molded gratings to see the durable and versatile products that come out of this process.
See the differences between molded & pultruded grating.
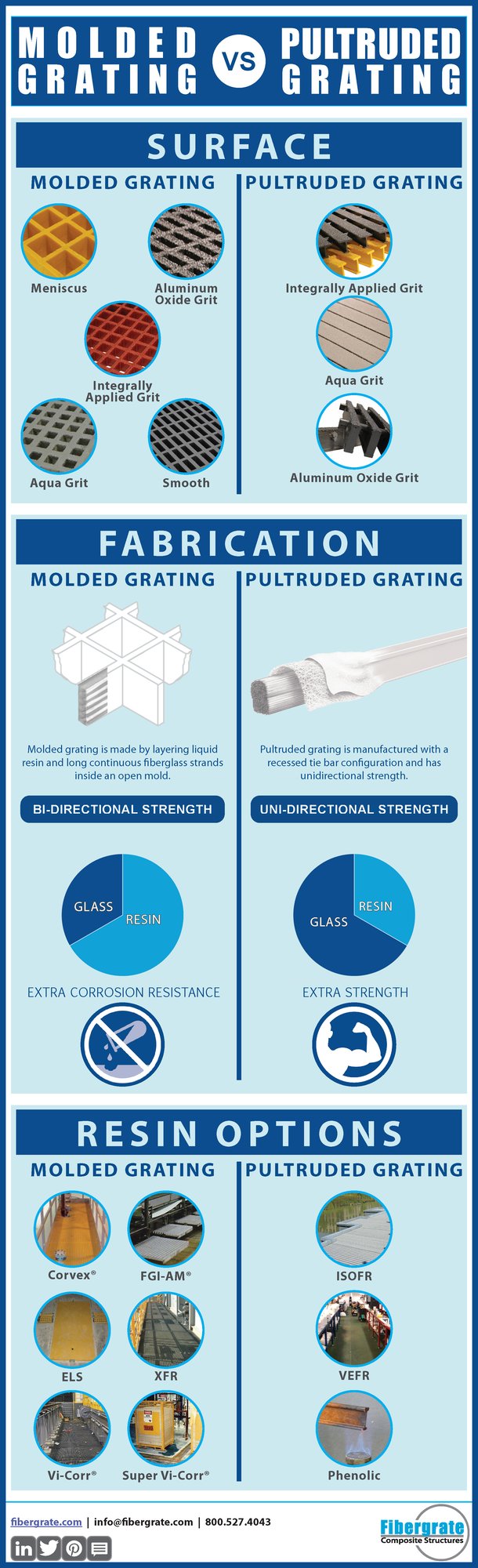
Molded vs pultruded grating infographic
What Additives Are Used in Fiberglass-Reinforced Plastic (FRP) Products?
Various additives are used to enhance the properties of FRP or aid in the manufacturing process:
- Fillers: Improve stiffness, strength, and dimensional stability.
- Pigments: Provide color to the final product.
- UV Stabilizers: Protect against UV degradation.
- Flame Retardants: Enhance fire resistance.
- Release Agents: Facilitate removal from molds.
- Thickeners: Improve resin application.
- Accelerators and Catalysts: Speed up curing.
- Modifiers: Enhance specific properties like impact or chemical resistance.
- Antioxidants: Prevent resin degradation.
The specific additives and their concentrations should be carefully selected to meet the unique requirements of each project.
Fibergrate's Fiberglass Reinforced Plastics
At Fibergrate, our FRP products are proudly manufactured in North America at our facilities in Texas and Mexico. We adhere to stringent quality control standards to ensure our customers receive the highest quality FRP products for their diverse applications.
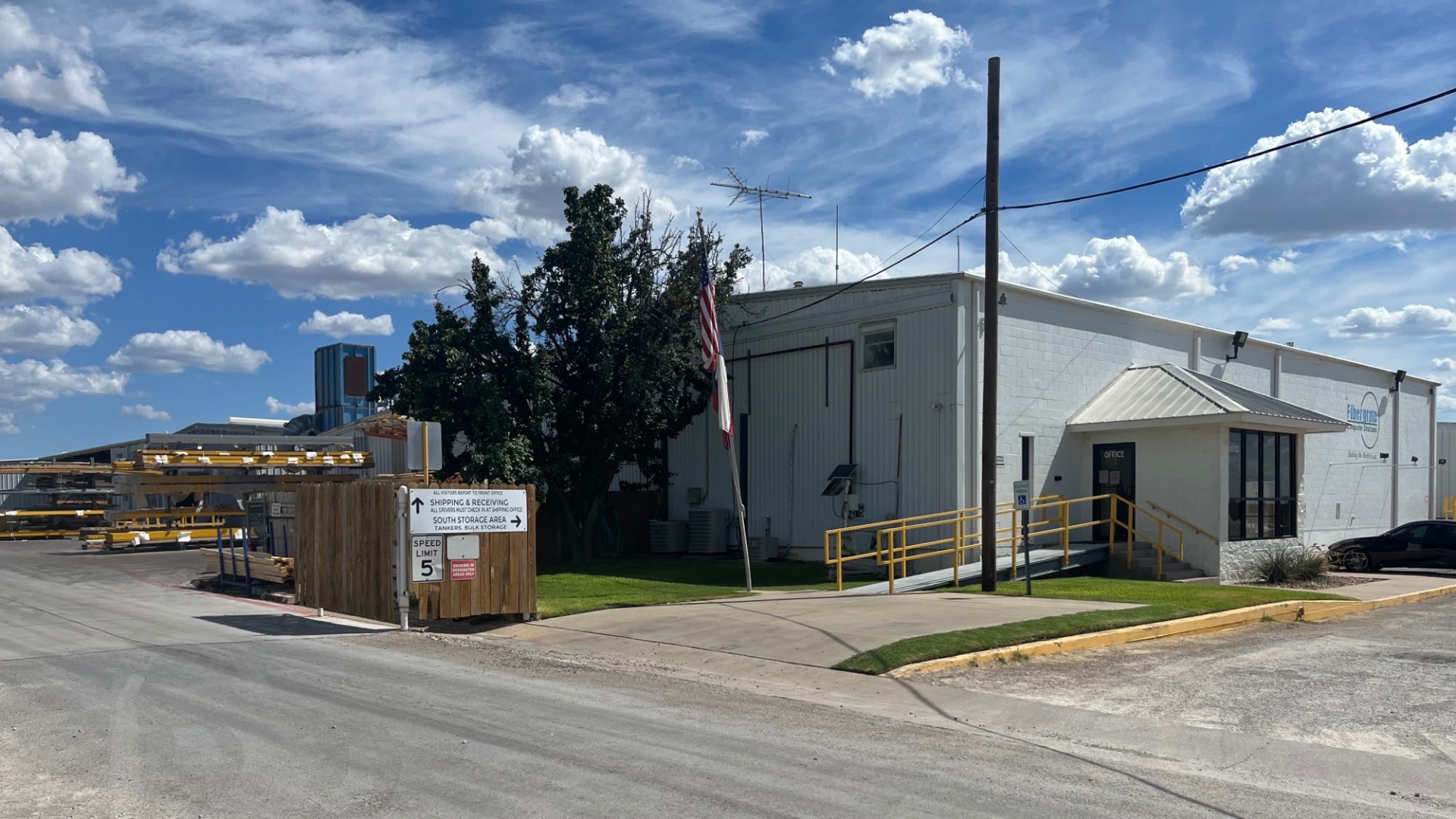
Fibergrate manufacturing location
We hope this overview answers some of your questions about fiberglass reinforced plastics. If you would like to learn more about FRP and its applications, explore our full catalog of FRP products or contact our experts for personalized help.
Topics: FRP, Fiberglass Reinforced Plastic